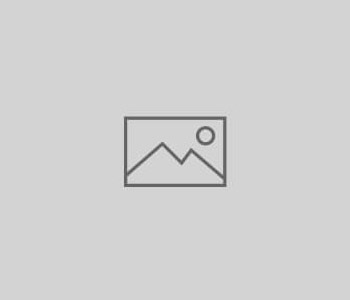
Understanding the Differences Between Mass Production and Batch Manufacturing…
Under the custom production process, the furniture shop receives a custom order from a client. They plan the project out, identifying the manpower, materials, and machines needed to complete the project. The project is then built to a predetermined set of specifications and delivered to customers on completion.
Although CM technology has been in place for decades in other industries such as commodity chemicals and food processing, there has been limited experience with it in the pharma industry. As a result, significant uncertainty over the all-in lifetime costs of this technology for specific applications, products and manufacturing scale remains. Continuous processing is generally more cost-effective for large-scale production due to lower labor costs and increased efficiency.
Know: Batch Processing vs Continuous Production
Similarly, the raw materials needed for a particular batch of products can only move to the next stage after all materials within the batch have moved through. That’s why the term “semi-continuous processes” was coined to describe activities that combine both batch and continuous processes. Materials are processed in batches but then linked together in a continuous sequence. This means no breaks in the production process, and materials are constantly fed into the system. While batch manufacturing offers numerous advantages, it also presents some challenges. Setup times between batches can lead to increased production costs, and product variation is risky between different batches.
- Both batch and continuous processing can be environmentally sustainable options by optimizing production efficiency and reducing waste.
- Also known as process manufacturing, batch manufacturing involves large quantities of raw materials being processed in batches through the production process.
- By producing goods in large quantities, companies can achieve economies of scale, reducing the cost per unit.
- The equipment used in continuous processes is often designed to monitor the work in real time, allowing for immediate detection and correction of quality issues.
- To ensure product consistency, manufacturers should carefully monitor and control their chosen processing method.
- However, batch processing can also achieve high levels of consistency if the process control is well managed.
Overall, the biggest difference between continuous flow and batch processing in manufacturing is how many products go through the process together. In batch processing, because entire batches are processed at once, it’s harder to have good quality control. Because one product is completed at a time, checking the first product and then adjusting the process if needed allows for defects to be easily prevented. However, because of the decreased cost, increased quality, and increased productivity, continuous flow is usually the better choice in most applications. Advanced monitoring systems and real-time quality checks ensure that output consistently reaches its maximum potential.
Most Affordable Maintenance Management Software
Track inventory in all your locations and set reorder points to minimize the risk of a supply shortage. Seeing that the quantities in continuous processing are much larger, it’s essential to quickly catch any deviations from the standard to reduce waste. Since each batch is produced separately, any quality issues can be identified and corrected before this batch is sent to retailers and the next lot is started. For example, a bakery may inspect each batch of bread, ensuring that the texture, color, and taste meet their quality requirements before being sold to customers.
By reducing idle time and minimizing unplanned stops, micro stops, speed losses etc. manufacturers can adhere more effectively to their schedules. While batch processing can lead to underutilization of resources, resulting in lower Overall Equipment Effectiveness (OEE) and Total Effective Equipment Performance (TEEP), it offers an advantage in quality control. Quality checks can be conducted at each stage of production, and in the event of a quality issue, contamination is limited to the affected batch, minimizing the risk of broader reproduction. The manufacturing processes we covered in this article are a fundamental part of manufacturing success. With the right business management tools, production processes, and an emphasis on lean manufacturing, you can achieve stability and consistent growth for your company and the industry, one customer at a time.
- A batch process involves executing production tasks in a predefined sequence to complete a specific customer order.
- For process improvement, a variety of advanced technologies are available to pharmaceutical manufacturers.
- Strictly Necessary Cookie should be enabled at all times so that we can save your preferences for cookie settings.
- Seeing that the quantities in continuous processing are much larger, it’s essential to quickly catch any deviations from the standard to reduce waste.
- In addition, because all of the ingredients are mixed at once, it is easy to ensure that they are properly combined and that the final product meets all quality standards.
- In terms of ease of automation, batch process is relatively more difficult than the continuous process.
- Batch processing provides better traceability and control over quality since the entire batch of ingredients is mixed at once.
This not only reduces waste but also enhances the overall sustainability of the production cycle, aligning with modern environmental standards. However, batch manufacturing can lead to longer lead times and increased inventory costs, as raw materials and finished goods must be stored in larger quantities. Additionally, the setup times for different batches can be time-consuming, which may reduce efficiency. The need for careful inventory management becomes crucial, as excess stock can tie up capital and increase storage costs, while insufficient stock can lead to missed sales opportunities. Balancing these factors is essential for manufacturers to maintain profitability and meet customer expectations.
Batch Process vs Continuous Process for Pharma Manufacturers
Maintenance is typically performed periodically, depending on the production schedule. However, since each production run involves starting and stopping the process, the equipment may experience more wear and tear, requiring frequent maintenance to ensure it operates correctly. This year, I spearheaded a research effort at the University of Maryland’s Robert H. Smith School of Business to answer that question. To learn more about batch process vs continuous process or how our Digital Factory Platform can revolutionize your operations, feel free to reach out to us. Consistently improving FPY over time enhances quality management maturity, strengthening relationships with clients and bulk medicine purchasers by demonstrating a commitment to excellence.
What Is Return on Investment (ROI) for Predictive Maintenance…
In case of deviations from the standard, the material and equipment can be adjusted to ensure the next batch has a higher quality. Further, when U.S. tax rates were raised to 28%, investing in U.S. batch facilities was no longer viable compared to investing in batch facilities in China and it reduced the attractiveness of investing in U.S. Continuous manufacturing has generated buzz in the pharma industry for years. Some large pharmaceutical manufacturers have even piloted continuous manufacturing (CM) under the U.S. Mass production is a method of manufacturing characterized by the large-scale production of standardized goods using assembly line techniques.
These two types of processing may look different in different industries, for example, manufacturing drugs in the pharmaceutical industry vs. processing liquid waste in the mining industry. However, the similarities and differences between the two types of material processing remain the same, no matter the application. Let’s dive deeper into each type of processing to understand their advantages and disadvantages. AI-powered quality control systems can continuously monitor production lines, analyzing vast amounts of data in real time. This allows manufacturers to identify issues as they occur rather than discovering problems after products have already been completed.
Think About Your Production Timeline
However, batch processing can be more economical for smaller production volumes with varied products. For a continuous process (figure 4) as the process is ongoing materials are feed continuously into the system and products, by-products and waste stream the system without interruption. Unlike batch systems cleaning is infrequent and is done rarely when there is a plant shutdown or maintenance. Examples of continuous processes are; oil refining, chemical manufacturing, fertiliser production, power stations, wastewater treatment and many others. Batch manufacturing offers greater flexibility, enabling manufacturers to switch between different products or formulations with relative ease. This adaptability makes it an attractive option for businesses looking to diversify their offerings.
In a batch process, the data can be used to analyze past batches and to identify purchase patterns and trends. However, in a continuous process, Katana’s data insights can be used in real-time to improve business performance. A batch process involves executing production tasks in a predefined batch vs continuous sequence to complete a specific customer order. But what if you need a production process that’s designed to produce consistently?